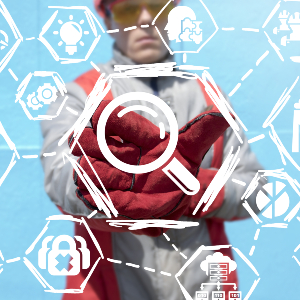
In recent years, the consumer demand has changed significantly and for which the manufacturers are buckling up. Manufacturing analytics has become imperative for the manufacturing industry to keep up its production quality, increase performance with high-profit yields, reduce costs, and optimize supply chains.
Manufacturing analytics implies collecting and analyzing data from different systems, machines, IoT devices, and exploring it in real-time to bring out insights critical to the smooth functioning of a manufacturing unit.
Traditionally, manufacturers could not capture and utilize all the data generated by end-to-end production lines. This involves the supply chain movement, production, and delivery. They had to juggle between complex systems and mechanisms to bring this data together. Utilizing the data generated by end-to-end production lines was a lengthy and time-consuming process.
Understanding Manufacturing Analytics
Manufacturing analytics turned the tide and made the whole process seamless and fast. The data exchange and automation lead to the speedy progress of manufacturing units. Predictive manufacturing analytics, big data analytics, Industrial IoT, network virtualization, and machine learning are all used in manufacturing analytics to create better and scalable production solutions.
Manufacturing analytics is specifically designed to collect and analyze data from different sources through sensors present in the machines to discover opportunities for improvement. The process extends from machines to humans, from an incoming order through its delivery; data is collected and reformatted in an easy-to-understand layout to highlight where problems exist throughout the process.
In simple words, it collects and manipulates data in more significant amounts to show insights that can boost the performance. Business users can also get automatic business reports to respond in real-time.
Why Do We Need It?
We all know that in a manufacturing unit, to keep up production quality, increase performance with high-profit yields, reduce costs, and optimize supply chains, we need to utilize all the data generated by end-to-end production lines. This is precisely why manufacturing analytics is needed.
Data analytics involves the use of advanced methods like classification, regression, etc. The data that’s in the collection process acts as a source that helps in determining our goal, making it clear to understand the cause-and-effect relationship between the information that’s achieved and the progress that’s made.
With manufacturing analytics, you can save energy while reaching the targets and improve the operation process to get to those targets with ease. This can even help you identify the issues, such as predicting a defect in the machine that would happen next week. Thus, saving time and money to maintain the effectiveness and efficiency of the business.
Benefits
The list of benefits of analytics is endless in the competitive business industry. However, a few are as follows:
Understand the supply of manufacturing chain:
The purchase of raw materials is a part of the day-to-day functioning of any manufacturing business. Optimizing the procurement can optimize the business outcomes. Data analytics will assist you in making better decisions by showing how each factor affects the result.
Manufacturing data analytics may make you realize the effectiveness and efficiency of every unit in a manufacturing life cycle, from your suppliers’ trucks through the end of the line. The analytics identifies the components of the machine which are continuously malfunctioning or are not performing as expected in a manufacturing unit.
Self-sustainable system:
Manufacturing systems operate without halt or interruption, which can lead to break downs and other issues. The problem is most businesses take action after the incident occurs.
Companies with the use of manufacturing analytics can examine their own need for repairs on a regular basis. This enables systems to repair on time and offer early warnings about more complex issues to resolve. Moreover, data analytics can reveal which components fail most frequently, allowing you to transform the problems into solutions.
Create better demand forecasts for products:
Manufacturers’ products aren’t simply made for the present; they’re also made with the idea of meeting future demand in mind. Demand is essential for a production chain since it might be the difference between a successful sale and unsold products inventory. Forecasts for most businesses are based on historical values from prior years rather than on more useful forward-looking data.
On the other hand, businesses may integrate current data with predictive analytics to provide a more exact estimate of customer demand. These predicted insights are based not just on prior sales but also on processes and how effectively operation lines are running, resulting in better risk management and lower production waste.
Better warehouse management:
After developing the product, they get ready to be shipped and are stored in warehouses. Running warehouses entails more than just finding room for things to be manufactured and stored.
With manufacturing analytics, one can establish efficient organizational structures, improve order flow and lower production costs. It is easy to comprehend how to enhance the inventory and manage warehouses using advanced analytics.
Increased customer satisfaction:
In any business, we need to understand what the customer wants. To accomplish consumer needs, analytics plays a major role by collecting the data through feedbacks, which can help in making the process more streamlined and as per customer’s requirements.
Once data is collected, the manufacturer can analyze it to determine the similarities and differences amongst consumers and segment them for providing more personalized services. This can help in increasing customer satisfaction and maintaining brand loyalty.
Manufacturing Analytics Use Cases:
Predictive maintenance:
Analytics utilizes aggregate data from real-time detectors on equipment, components, or machinery to predict when they need to be replaced or whether the machines functioning outside normal limits. This is useful in determining the likelihood of machine failure or equipment defect.
The analytics in such a case can also help us understand the capacity of a plant and how many units of goods can be produced in each cycle, therefore being helpful in its capacity planning. Through analytics, a choice can be made for the optimal number of units to produce over a given period, considering capacity, sales forecasts, and parallel schedules.
Predictive analytics tools may send out automatic maintenance requests as well as receive automated readings. As a result, the process becomes short and reduces maintenance costs.
Demand forecasting:
Combining the data of market history with respect to a few high impact variable algorithms, you can explain a lot of variabilities that can help in planning for significant capital spending or brief breakdowns. One such example is the seasonality of consumer products, like ice cream in the summer or cold-weather clothing in the winter. Thus, using data of market history combined with the data of a few high impact variables can explain a lot of variabilities and can help in planning significant capital expenditures or temporary shutdowns.
Demand forecasting is not a new concept for factories throughout the world, but predictive analytics adds robust statistical algorithms to the mix. Predictive analytics can account for complicated elements such as customer purchasing habits, raw material availability, trade war ramifications, weather-related shipping circumstances, supplier concerns, and unanticipated interruptions.
Effective utilization:
If the machines are on their optimum usage, then the data generated as insights can help us to understand what practical measures can be taken to improve the business unit’s performance.
Data analytics assists you in understanding the cost and efficiency at every stage in the production cycle till the time the product reaches the supplier’s truck.
Managing supply chain risks:
We know that the supply chain can be unpredictable, and that risk is always involved in a manufacturing process. In the above-mentioned situations, big data analytics helps manufacturing companies in predicting potential delays and accurately calculate and determine any problem beforehand.
Conclusion
As times are changing, businesses should also change. The implementation of analytics in the manufacturing sector has changed the shape of the business industry and has saved it from potential risks besides improving the production lines. The path for Industry 4.0 has already been carved. It is not the question that whether companies will adopt analytics or not. The question is when they will adopt business intelligence. Because the path to the ultimate Industry 4.0 goes passes through analytics and without it the data collected by the intelligent IoT devices is pretty much useless. The faster the adoption, the faster companies are stepping ahead of the competition. Though the manufacturing sector has one of the highest rates of BI adoption, the journey is long. The biggest names in the industry are definitely on board with the IoT and analytics bandwagon, but the medium and smaller-sized companies still need to amplify their game. With technologies like cloud and Analytics as a Service, companies do not need to invest heavily in analytics initially. They can simply test the waters and see the powerful insights and the benefits it can reap and then can adopt on a larger scale. With the power of self-service analytics, the business users will be empowered to not just understand their data but also to make time-sensitive decisions right on time. The future for sure is data-driven and the success shall favor those who are prepared for it.