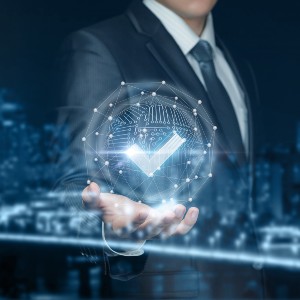
As proponents of Lean Thinking, we view corporations as data factories that produce information for operations, reporting, and financial modeling. We treat data as inventory, data management as manufacturing, and business output as finished goods. The goal is to go from inventory to finished goods with as little waste, cost, and risk as possible. Anything that does not add value is considered waste. Wherever there is waste, there is risk. Taking the conceptual leap from the car factory to the data factory opens the doors to revolutionize Data Governance.
This column is the first in a quarterly series that defines how corporations can remove the bureaucratic bloat that creeps into Data Governance. This applies to organizations that are new to Data Governance, as well as those with fully entrenched governance implementations. The latter of which tend to stagnate under the pressures of excessive organizational policies and procedures.
The methodology we use to eliminate different types of organizational waste in Data Governance comes from a strange place, the factory floor of an automotive manufacturing plant. Believe it or not, the assembly line of a car factory has a lot in common with the production and management of data.
The key is Lean Production. From the groundbreaking achievements in automotive manufacturing came advancements in Lean Thinking, Six Sigma, Quality Circles and the application of System Thinking to solve complex manufacturing problems. In that world, Lean Production was responsible for a 50 percent reduction in the areas of manual labor, manufacturing space, investment tooling, engineering hours and time to new product development.1 All this was accomplished through teamwork, communication, efficient use of resources, elimination of waste and continuous improvement.
It all started when Japanese engineers observed tremendous waste, termed muda, when visiting mass production facilities in the U.S. and Europe. They also found widespread inefficiencies and quality problems. Lean Production was their solution.
Lean Production, based on Lean Thinking, was widely heralded as a success because it focused on the elimination of waste on the factory floor. This included bureaucracy as measured by outdated KPI metrics and procedures, most of which did not add value to the customer or the corporation. In fact, most of the work beyond the actual manufacturing assembly contributed very little to the factory’s bottom line.
Many sacred cows were slaughtered having outlived their usefulness. As example, there was a standing rule that only a senior manager could stop the assembly line because the perceived impact on productivity was too great. This backfired as evidenced by the high volume of rework required – at a much higher cost – when defects were found after the car was completely assembled. Imagine the cost and effort to replace a defective bolt in a transmission after the car was assembled. Multiply this by the 1,000 cars that rolled off the assembly line every day.
Lean Production introduced radical changes to the factory. In this example, any factory worker had the authority to stop the line in order to replace the bad bolt the moment they saw the problem. Product quality was addressed on the spot rather than at post-production. Seems like a simple idea but it was extreme at the time, yet highly effective.
Let’s return to the world of Data Governance. One important point to make here is that Lean Production is not a synonym for Agile Production, as I often hear. Instead, Lean Production was a complete rethinking of how manufacturers could achieve peak performance by eliminating waste and making changes that add value to all stakeholders.
MetaGovernance specializes in Lean Governance. The approach provides a way to visualize waste in data manufacturing. The focus is on business value. We look with a critical eye at any task or activity that does not provide value to the consumers. Consumers in this case being data owners, data consumers and data stewards.
Corporate waste is a growing problem across data and reporting platforms despite the huge sums of money spent on system improvements. Today, we see similar problems when reviewing the state of client data and their reporting environments. The reliance on spreadsheets for collection, reconciliation and reporting creates a “perfect storm” for bad data. This also makes it nearly impossible to know the correct sources for all the data, compromising ownership and accountability. In theory, data governance implementations based on policies, procedures, and other governing documents are meant to ensure data integrity across the corporation. In reality, the best business processes, tools, and approaches to data management can still fail to meet that objective.
Lean Governance offers a fresh look at how data is used across the entire organization. The first step is to root out waste. This involves analyzing your data factory for bottlenecks, typically found among the use of spreadsheets in reporting, manual reconciliations, high data defect rates, data corrections outside of source systems, insufficient business glossaries, and limited awareness of correct data sources. We find that it’s impossible to achieve total data quality and operating efficiency unless you understand overall structures, patterns, and behaviors – and how they reinforce or hinder one another. The goal is to provide value to the end customers, both inside and outside of the company.
Lean Thinking started in Japan and moved its way to North America and Europe. The introduction of Lean Production required accountants and efficiency experts to rethink how they measure productivity. This was a hard-fought political battle. Large factories that would not change their bureaucratic ways were ultimately closed. The General Motors plant in Framingham, Massachusetts, is but one example in the factory graveyard.
As Data Governance professionals, we have the opportunity to replace bureaucratic waste and inefficiencies with new lean principles. We can use many of techniques that revolutionized manufacturing to optimize a corporation’s data factory. Lean Governance requires solving the right problem through systemic understanding of the flow of data to maximize value and eliminate waste.
This column focused on practical solutions on how to identify and eliminate waste within governance implementations. The ultimate winner of this journey will be the corporate stakeholders, both internal and external to the organization, for they are the true customers of the data.
[1] The Machine that Changed the World. Roos, Womack, and Jones.