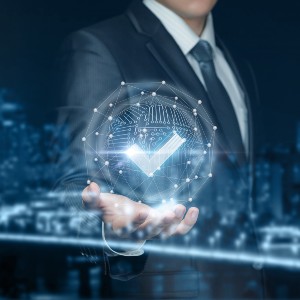
Lean Governance is a proven method to stop burning your company’s cash. This approach is all about saving money by eliminating waste across your data factory. The data factory represents all activities related to the creation, processing, storage, and usage of data for operations, reporting, analysis, marketing, and a myriad of other business activities. The goal is to process raw data into high quality finished goods with the least amount of waste, risk, and cost.
Data management waste is an industrywide problem. We have witnessed it firsthand among our diverse set of clients. In the world of data processing and reporting, this translates into added expense, robbing the core business of investment opportunities. Think of it as a waste tax.
Here are some of the ways we’ve seen companies needlessly burn cash:
- Companies pay millions in extra audit fees because the external auditors or regulators do not trust their reporting. This can go on for an extended period of time until accuracy is verified.
- Staff spend 20% of their time collecting and reconciling data either because the correct source is not identified, or they don’t trust the data.
- Multiple departments reconcile the same data on a daily basis using spreadsheets because there is neither clear ownership nor automated reconciliation tools.
- Accounting has to re-run monthly reports because they were started before the data was clean.
- Significant fines and reputational impact caused by confidential data leaks.
- Financial restatements due to bad data.
This waste and inefficiency can add up to millions of dollars. And unfortunately, resolutions to these problems are done in triage mode until the originating crisis is over, then things return to the sub-optimal norm.
Our blogs on Lean Governance have focused on the simplicity of Lean Thinking. The groundbreaking advancements in manufacturing were largely accomplished through common sense and knowing how to solve the right problem.
Let’s use Lean Manufacturing to explain how to stop burning cash in data processing. On the factory floor, the inventory used in the manufacturing process is part of working capital. This includes raw materials (like steel), work-in-process and finished goods (like car parts). The goal of Lean Manufacturing is to deliver a quality car (with zero defects) to a satisfied customer at the lowest cost.
The brilliance of lean was that it focused on inventory. Traditional theory of mass production stated that economies of scale would maximize profits. Bigger machines with higher throughput. Unfortunately, assembly of components could not keep up with production. As a result, raw materials and work-in-process inventory accumulated on the factory floor and in warehouses.
There is a Systems Thinking archetype called “Fixes that Fail.” In this example, expensive computer scheduling and forecasting systems, and their operational staff, were implemented to deal with inventory bottlenecks and product shortages. But these fixes failed to solve the problem. In fact, they added costs for storage, transportation, and retooling.
Lean Thinking was the answer to making products with zero defects with real cost savings in materials, shorter delivery times, less rework, and satisfied customers. The game plan had five areas of focus:
- Precise definitions of quality expectations
- Clear product classification schemes
- Only have inventory needed for small cycles (less is more)
- Quality controls along the factory floor to fix problems at the source
- Reduction in computer and manufacturing costs
Let’s move from the factory floor to the data factory of a typical organization. The most noticeable similarities are the concept of inventory. Instead of steel we have data – the lifeblood of all companies. Instead of sub-components we have derived measures and other types of information. Instead of cars, we have reports, disclosures, and customer statements.
To illustrate how the above approach can eliminate waste in your data factory, we’ll use the example of producing an SEC 10-Q quarterly report.
1. Precise definitions of quality expectations
The SEC, GAAP and other accounting standards publish precise guidelines on disclosure requirements. Regulators publish advisory bulletins and examination manuals with their interpretation of the standard. Data reporting teams can use these guidelines to ensure they have the needed data, calculations, and verifications implemented.
2. Clear product classification schemes
Data Governance implementation should always start with creating the classification scheme for company’s data. Grouping, security classification, and retention requirements are part of this scheme. MetaGovernance clients typically have 10,000+ unique business attributes. These attributes are grouped into subject area (domains), then the characteristics are defined at the higher level. Attributes are then associated with the subject area. This is all governance metadata that needs to be stored in a database, not a spreadsheet.
3. Only have inventory needed for small cycles (less is more)
Just how many copies of the same data does a company need? How many piles of the same inventory product does a factory floor need? The answer is the same. Every business attribute should have a clear system of record. Copies for processing efficiency and history (e.g., Data Warehouse) can store an additional copy. But we see 10+ copies of the same data across the organization due to lack of architecture and planning. Not to mention what we find in spreadsheets. This is pure waste and risk.
4. Quality controls along the factory floor to stop issues upstream
Data moves throughout the data factory from source systems to Data Warehouse. Automated reconciliation should be implemented to ensure that the correct number of rows and data have been moved. Verification against an additional source (e.g., General Ledger) provides confidence in data accuracy. Effective Data Governance includes a metadata model for awareness of the ownership and consumption of specific subject areas of data is known. Reconciliation results are sent BEFORE the work of report production begins. Waiting for Internal Audit (3rd line of Defense) or External Audit (4th line of Defense) to find an issue is way too late, resulting in rework, risk, and, of course, cash burn.
5. Reduction in computer and manufacturing costs
Companies that have their inventory under control realized that they could actually eliminate production machinery and decommission computer systems. For Data Governance, companies often buy tools before the true need is known. We see this in countless unused metadata tools that helped developers but offered little to business and audit functions. When you streamline data processing, eliminate multiple copies of data, get rid of the spreadsheets, and have clear awareness of the source and use of data it is possible to do more data processing at a lower total cost. Staff and technology resources can be redeployed in higher value areas of the core business.
Lean Governance is designed to root out waste. If you suspect that your company’s data management function may be burning cash, contact us to learn about solutions.