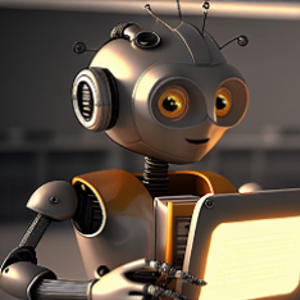
There’s no denying it. The digital revolution we’re living through has fundamentally changed how business is done. So much so that digital platforms and applications now drive enterprises of all kinds.
Some like to call this unabashed modern digital age the ‘fourth industrial revolution’ — or, if you prefer, ‘Industry 4.0’. Yet, whatever you call it, this IT-driven era seems to be behind practically every new business innovation — from transforming IT-derived communications to bringing wholesale digitization to the maintenance of equipment and machinery assets. Indeed, this strikingly modern asset maintenance approach, aptly called “predictive maintenance”, is becoming ever more popular.
To get an idea of just how big a deal it’s become, consider the fact that, according to Polaris Market Research, predictive maintenance’s global market was worth $4.16 billion in 2021 (see chart below).
Not just that, but Polaris expects the industry to grow by a compound annual growth rate (CAGR) of 30.9% up to 2030.
This article, therefore, will examine not just what predictive maintenance is, but also how it is being driven by Industry 4.0 — and why it’s proving so beneficial to businesses the world over.

Click to view larger
What Are Reactive and Preventive Maintenance?
So, to truly understand why predictive maintenance is such a game-changer, we first need to go back and explore what preceded it.
Initially, there was reactive maintenance. This was a universal approach to asset maintenance that saw assets repaired or replaced only after they had worn out.
A bit like, for instance, replacing a years-old business telephone system with a new call center system when the phones themselves have stopped working.
Eventually, to improve efficiency and cut costs, this model was superseded by preventive maintenance. The onus had now shifted to trying to prevent equipment from failing before its expected End of Life (EoL) by servicing it at regular intervals.
A proactive approach, preventive maintenance relies on regular inspections of an asset, scheduled according to the asset’s expected lifetime.
What Is Predictive Maintenance?
While preventive maintenance has long since established itself as the dominant maintenance approach, a fundamental flaw in this approach has become obvious over time.
Too often, preventive maintenance fails to achieve Overall Equipment Efficiency (OEE) because it wastes time, manpower, and costs on the maintenance of assets before they require servicing and repairing — which means before they begin to decline and get near their EoL.
In which case, to improve OEE results, business leaders realized it would be better to plan maintenance around when an individual asset needs attention. But would this be possible?
Well, this is where predictive maintenance comes in.
Instead of safeguarding asset-use via regular maintenance intervals based on hypothetical EoL estimates, predictive maintenance alerts enterprises when individual assets require attention based on far more accurate information.
This happens via Big Data analysis, which allows for continuous, real-time digital monitoring of assets.
Analysis of all this asset data, then produces more precise predictions of individual assets’ lifetimes and when they require maintenance.
In turn, this enables companies to save on unnecessary equipment costs and manpower, while at the same time assuring customers that assets always abide by industry standards (on occasions when they might ask themselves questions like, “What is ISO compliance?”)
How Does Predictive Maintenance Fit with Industry 4.0?
Now, despite its undoubted benefits to businesses and customers, predictive maintenance is yet to usurp preventive maintenance as the most relied-on approach for sustaining assets.
Yet, the signs — not least its global market growth — are that predictive maintenance is on the march. The reason for this is that today’s ongoing digital revolution is facilitating its uptake right across the globe.
It’s thanks to the digital proliferation of Industry 4.0, therefore, that predictive maintenance is thriving.
Using the innovative tech of Big Data, automation, AI, AR, and advanced sensors, predictive maintenance draws on different innovations of the Industry 4.0 age to ensure the management and upkeep of machinery and equipment is more effective and efficient than ever before.
Plus, it doesn’t hurt, of course, that other Industry 4.0 innovations — such as easy data sharing among stakeholders and superior digital communications (via the likes of VoIP support) — can further, if indirectly, enhance the efficacy of predictive maintenance.
How Does Predictive Maintenance Work?
Broadly speaking, predictive maintenance manages assets thanks to specific IT applications, which are directed by many different sensors that monitor the health of the assets.
These sensors collect masses of data so the condition of each individual asset can be assessed and acted on via sensor data analytics.
Meanwhile, from the perspective of a maintenance technician, the condition of an asset can be immediately and easily ascertained via a visualized dashboard.
This visualization doesn’t merely give a technician the information they need to know about an asset’s health, it advises them, too, on what next steps should be scheduled and the work required to maintain, repair or otherwise address the asset.
What Are the Predictive Maintenance Applications?
Now, to dig a little deeper into the Industry 4.0 innovation at the heart of predictive maintenance, let’s take a look at the IT applications that ensure it can successfully take place
- Intelligent Control Functions
The flexibility of automation and control functions ensures different control modes can be deployed in different scenarios, depending on what is necessary for individual machinery and equipment assets. For instance, should a technician discover an asset is in the early stage of degrading, they would simply select a specific control mode to ensure operations cease or are slowed to the extent that the asset’s Remaining Useful Life (RUL) will be extended. Needless to say, these flexible functions and the applications that drive them are further enhanced when the applications are improved via an application modernization strategy. This serves to safeguard the health of the applications, the health of the control functions, and, by extension, the health of the assets. - Root Cause Analysis
What’s causing an asset to degrade? By tracking the health of an asset over its lifetime, this application can highlight potential causes behind the issue. In some instances, Root Cause Analysis may deploy AI algorithms to unearth hard-to-identify degradation that would otherwise go unknown when relying on domain knowledge alone. Quite clearly, then, in terms of AI’s use in business today, it’s not just about image creation and chatbots in AI — AI is driving many different breakthroughs. - Future Condition Simulation
An application that helps engineers figure out what operations will best preserve an asset’s lifetime. This one sees the deployment of Digital Twins tech to help simulate an asset’s behavior as it ages. This means, therefore, that the correct maintenance option to prolong an asset’s OEE can be identified. - Maintenance Schedule Optimization
This application ensures the work schedule for maintaining assets is organized as smartly and effectively as possible. It uses asset data along with business process insights to inform an automated decision on when maintenance will best maximize OEE. - AR Remote Maintenance
The last of the predictive maintenance applications of note, this one enables the leveraging of augmented reality (AR) to help plan remote maintenance processes. This means that a customer can be supported or assisted by an original equipment manufacturer (OEM) in maintaining or repairing the asset, without the OEM having to be on-site. As a result, this saves costs for the OEM and time for the customer. In simple terms, therefore, this application ensures an asset is correctly maintained via augmented reality visualizations — instructions and data appear over the top of a cyber-representation of an asset. So, it provides an easy-to-follow visual guide that represents the very cutting-edge of Industry 4.0-driven predictive maintenance.
The Benefits of Predictive Maintenance
In contrast to reactive or preventive maintenance, predictive maintenance offers enterprises and organizations several enhanced benefits.
- Advanced Maintenance Planning
Maintenance costs are minimized and the bottom line maximized because predictive maintenance uses digital innovations, such as wired and wireless sensors, Big Data, AI, and automation, to enhance the planning of maintenance tasks. Indeed, these components combine with other Industry 4.0 components like DevSecOps cybersecurity to ensure front end and back end operations combine smoothly and securely. - Fewer Downtimes and Significant Time Savings
Owing to its improved planning of asset check-ups and repairs, as well as more efficient and quicker maintenance operations (including the use of AI-driven automation and AR-derived visualization), predictive maintenance minimizes unscheduled downtimes and reduces the duration of all downtimes. - Better Use of Assets and Better Quality of Service
Overall, predictive maintenance can help enterprises and institutions make the best possible use of their assets and deliver the best possible service to customers.
The Bottom Line: Predictive Maintenance Is the Future of Asset Maintenance
Industry 4.0 has radically altered the asset maintenance game.
In addition to changing much of the business world beyond recognition — from online sales and bookings to faxing without a fax machine — Industry 4.0 has launched asset maintenance forward.
The result is predictive maintenance. Its ever-growing popularity is testament to the fact it’s the way ahead in the upkeep of equipment and machinery.
With its capacity to use ground-breaking data analysis, automation, AI, and AR to maximize maintenance planning and asset preservation, predictive maintenance can extend asset lifetimes, reduce servicing downtimes, save costs, satisfy customers, and boost bottom lines.
In other words, it’s the future of asset maintenance.